PET, thanks to its characteristics of lightness, resistance and transparency, is an ideal material for the packaging of food sauces.
Its oxygen and moisture barrier allows you to preserve the flavor and aroma of your products, while its versatility allows you to create packages of different shapes and sizes. In addition, PET is recyclable, making it an eco-friendly choice.
Starting from these assumptions, within this article we will analyze SIPA and the Turkish converter Özler Plastik case history, identifying the company's production needs, the reasons that led it to choose SIPA, the technology adopted and the growth results obtained.
About Özler Plastik
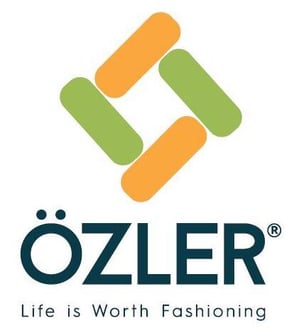
Özler Plastik, founded in 1951, is one of Turkey's leading converters, specializing in rigid packaging and closure systems for both consumer and industrial applications.
The company operates six production plants in the country plus one in France and one in Spain, as well as more than a hundred global delivery points, thus covering the needs of many companies around the world.
Özler Plastik has an in-house R&D Technology Center, focused on product design, testing and development.
The company's initial needs
A few years ago, in the midst of the COVID period, the company needed to start the production of PET containers on behalf of a leading brand in the field of sauces, for single-layer and multi-layer containers.
Production had to be highly efficient, with minimal energy consumption, while ensuring high bottle quality.
Why choosing SIPA
After careful market research, Özler Plastik chose SIPA based on several factors. What counted first and foremost was the specific expertise in the production of special containers, such as those required by Özler Plastik, with hot filling, based on solid experience in linear blowing.
Added to this aspect is the strongly customer-oriented approach and an extremely punctual organization with regard to after-sales service, as there is a SIPA branch in Turkey.
The technological solution provided by SIPA
SIPA has supplied Özler Plastik with an SFL DYNAMIC 4, the latest generation for its stretch-blow moulding systems, for the production of single-layer and multi-layer bottles in three formats: 250 g, 400 g and 650 g, with an output of up to 5000 bottles per hour.
SIPA has introduced various improvements in terms of speed, versatility, productivity, energy efficiency, process sustainability and product quality, which, combined with the low maintenance cost, translate into operating costs among the most competitive on the market.
The pitch of the ovens is available in two sizes, for bottles with different neck diameters, offering the possibility of adapting the heating more precisely to the type of neck or bottle.
Productivity has increased by about 10% more than the previous generation. This means that an 8-cavity blower can produce 16 thousand bottles per hour, in sizes ranging from single-dose to 1000 ml.
The increased productivity is due to factors such as faster press movement and improved blow valves. Despite this significant increase in capacity, energy consumption is lower than in the previous generation.
READ ALSO: "SFL, SIPA’s PET blow moulding machine: excellence and flexibility"
The results achieved thanks to the partnership
Özler Plastik has been able to see the efficiency of the processes achieved by the SFL DYNAMIC 4. The results speak of stable production characterized by high product quality and first-class energy efficiency. Versatility is another strong point, since the machine allows you to produce a complete range of bottles of various sizes, with an output of up to 5000 b/h.