For some years now, the concepts of Lean Production and Lean Manufacturing have been introduced to all the most sophisticated world production systems.
As the name indicates, this is a lean form of production, aimed at the continual improvement of industrial processes wishing to adopt an organization based on greater profitability and increased efficiency, with lower costs.
Modern modular Lean Production systems make it possible to start from theoretical principles of continual improvement and reach concrete solutions in a much more efficient manner than in the past.
This is the case for SIPA, with particular reference to the production of complete, high performance injection moulds and hot runners.
READ ALSO: "Hot runner mould system & operating costs: alignment and cleaning"
The initial requirements for proper Lean Manufacturing: the integration of internal company departments
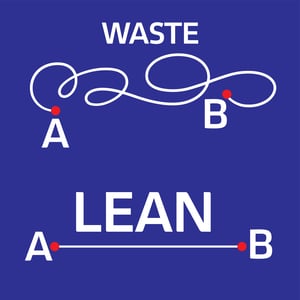
In order to achieve proper application of the principles of Lean Manufacturing, that is to say greater productivity, eliminating waste, it is essential that all the processes connected to creation of the moulds be united.
In other words: an efficient factory, with a single chain of responsibility for the whole manufacturing process.
Put into practical terms, this means that the individual sales representatives must be fully supported by the sales engineering department and by production. It is only in this way that all the information the customer may need will be present when the order is made.
A single IT platform for the process
From an information technology management viewpoint, it is extremely important that there be a single IT platform guiding the process, from design to production.
The various phases must therefore be united within a single scheduling system that allows them to be monitored.
All this means providing an Industry 4.0 set-up.
SIPA is organized in such a way that the various phases making up production of the moulds all take place as part of a single project.
This starts with design of the preform, then moves on to definition and processing of the raw material to create the moulds. The machine programs and quality control of individual pieces also form part of the same process, through the so-called closed loop system.
READ ALSO: "Case history: first SIPA Xtreme platform for lightweight PET preforms"
Everything that is produced must be traceable within the project and inserted onto the same platform.
Before delivery the mould is tested and then sent to the customer company.
Support does not end with delivery of the mould
As you can imagine, operations do not end with delivery of the mould to the customer.
The added value provided by SIPA consists of the full support provided by its technicians for installation of the latter in the destination system, start-up and process checks in the machine.
Lean management in SIPA’s China factories too
As well as its Italian headquarters and the other centres worldwide, SIPA also operates in China, with a factory in Hangzhou, a consolidated structure that has grown rapidly.
It is currently able to produce 300 blow cavities/month and 800 injection cavities/month. With local production of mould plates it is possible to produce a 144 cavity cold half in just eight weeks.
SIPA continues to improve its production, mould refurbishment and conversion capacity, while paying great attention to Lean Manufacturing to improve efficiency and reduce delivery times of its moulds.